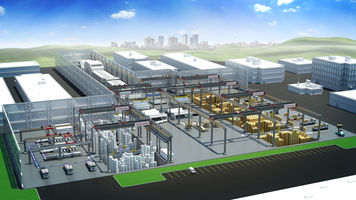
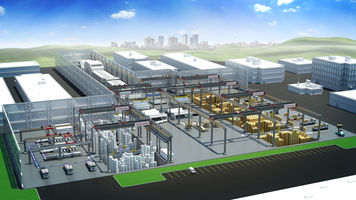
Maximizing the productivity
Pulp and paper is an industry tailor-made for automation. When it comes to choosing the right level of automation, it’s important to understand the nature of what you are machining as well as your specific requirements and capabilities. In several critical areas of the mill, automated cranes can help reduce labor costs, optimize storage, track inventory, reduce roll damage, increase productivity and lower the capital expense associated with forklift systems. Moving into the future, automation is taking an ever-larger role in promoting mill safety, productivity and profitability.
Semi-automation involves an operator picking the load and then pressing a button to instruct the crane to deliver it to a pre-determined destination. Our cranes already include many features to help maximize safety and productivity. Movements and cycles are automatically controlled, minimizing human error. Konecranes Smart Features help improve safety, cycle times and load positioning, delivering major benefits when performing repetitive actions and are particularly useful on automated cranes.
Smart Features for increased productivity
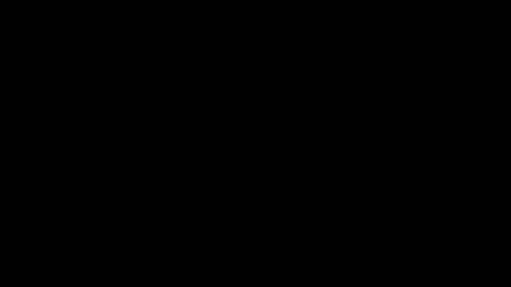
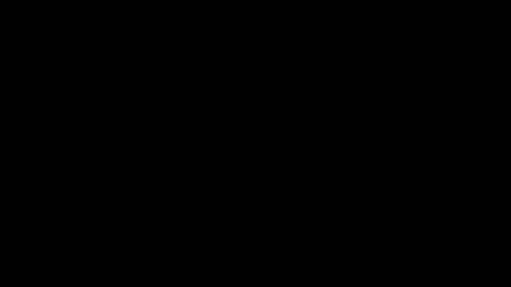
Sway Control
Sway Control limits load swing by controlling the acceleration and deceleration of the bridge and trolley, enabling faster load handling and more precise positioning. The operator can use full crane, trolley, and hoists speeds even while driving close to the walls, and the risk of grab damage is reduced.
A recent study confirmed that cranes with Sway Control are 60% faster than an ordinary crane.


Inching
Inching improves accuracy by allowing the operator to move the load in small increments of 2 mm to 100 mm. The crane stops after it has moved the set inching distance. Operators can set increments on the user interface when starting up the crane, with the possibility to program a different distance for each motion.
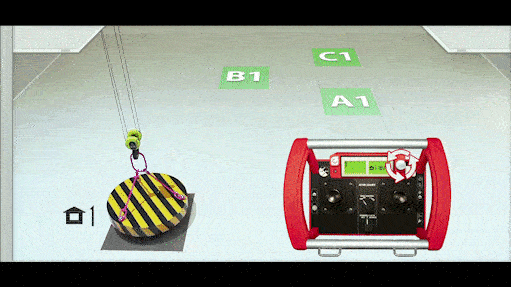
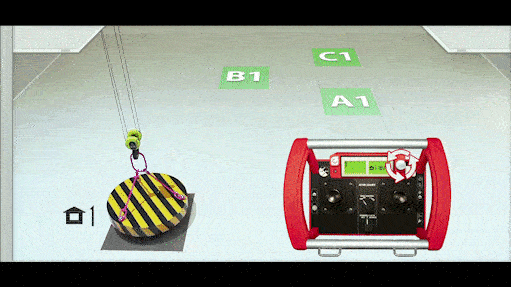
Target Positioning
Target Positioning moves the load from one of eight home positions to one of 120 possible preset target positions within a predefined area. The crane slows down, stops and lowers the load at the set target point. Just one button automatically returns the crane to its home location.
The Konecranes Target Positioning feature has been designed to reduce cycle times and to enhance safety.
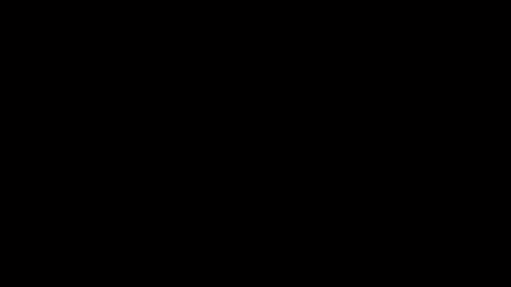
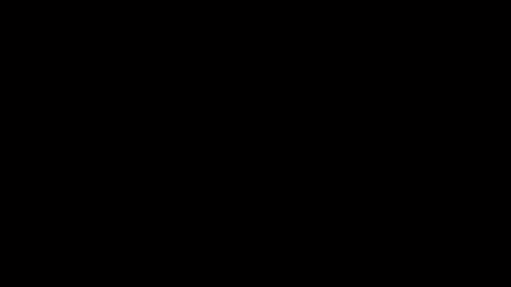
Protected Areas
Protected Areas can be used to assign spatial parameters for crane operation, automatically limiting crane movement to designated working areas only. Managers can pre-program no-go areas to keep the crane from going where it shouldn’t. This maximizes crane operation space while helping to reduce the risk of accidents, equipment collisions and load damage. Protected Areas allocates up to 16 permanent “no-go” zones to limit the crane’s movements to preset working areas.
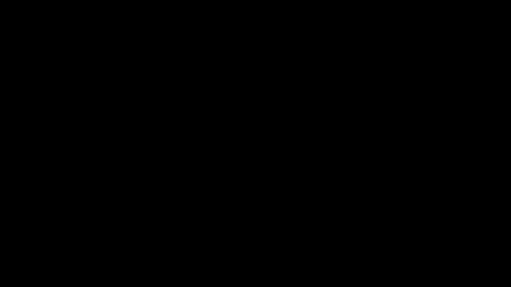
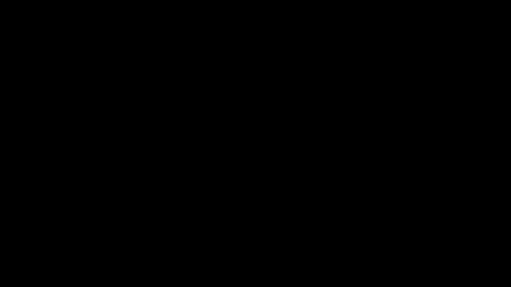
End Positioning
End Positioning allows operators to set the exact destination of a load and the outside area, or “window” for manual navigation. Once the operator brings the crane to the window, the End Positioning button automatically sends the crane to its final position. As a safety feature, the operator lowers the load manually to complete the movement.
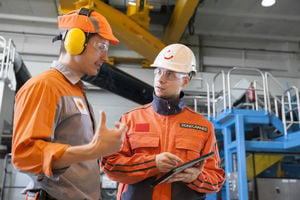
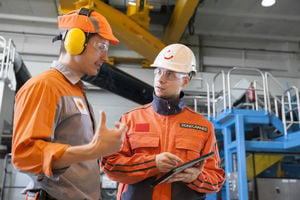
Automation helps protect people as well as products
ASRS systems are also designed to be safe around people. Access to the automated area is synchronized with crane operation, so that access is only allowed when the crane is set to stand-by state. Separate protected areas can also be set inside the normal operating area of the crane. The crane is synchronized with the conveyor control system by means of hardwired signals during material pick-up or drop-off. This maximizes the safety of material exchange and both systems can stop the process if there are any unexpected faults or alarms.
In addition, the cranes are equipped with safety features such as overload protection, over-speed protection, limits for crane motion and emergency stop functions. Konecranes automated cranes for paper mills are engineered to meet or exceed applicable international and local safety regulations.
Fully automated paper storage
Konecranes Automated Storage and Retrieval System (ASRS) can revolutionize productivity, especially in mills with limited space. ASRS combined with fully automated crane increases handling speed, stacking paper or tissue rolls much higher in less space than comparable forklift systems, without requiring floor space for aisles. The system accurately tracks the location of each bar-coded roll individually, assuring fresh inventory. And, up to 30 percent of the energy used to lower each load is recaptured by Konecranes DynAReg regenerative braking system. Electricity is fed back into the network and used to run other machinery, lowering overall energy costs and reducing environmental impact. Above all, mills using ASRS can eliminate the labor and capital cost of forklift systems.
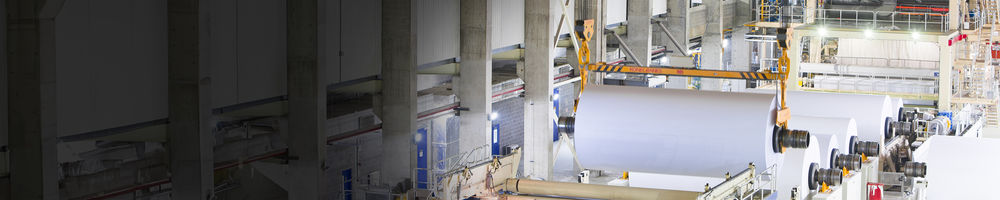
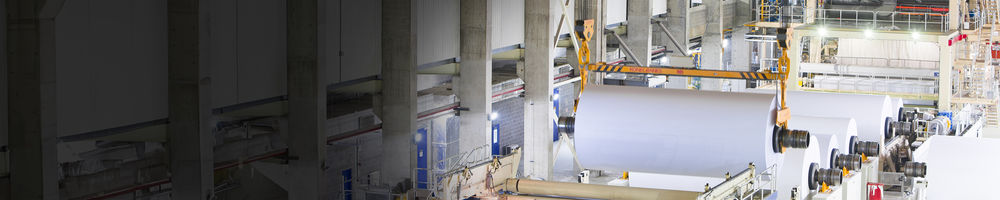
Automation in parent roll handling may pay for itself
Parent roll handling cranes can handle full rolls and return the empty shafts on semi-automatic mode to and from the paper machine pope winder. Using this approach, jumbo roll stands can replace expensive traditional conveyor systems. Lifting beam hooks with mechanical locking devices and positioning sensors provide better operational safety, in both manual drive mode and semi-automatic drive mode.
Safety is also improved because an operator does not need to be nearby–the crane works in a totally closed area. Eliminating the conveyor rails saves the mill far more than the cost of automating the crane, allowing mills to recover their investment sooner.
Automated train loading system
Konecranes newest automation innovation can move 1,100 tons of pulp per hour onto train cars. This fully automated system also fills a 1,400-ton buffer at the railway platform twice a day. The cranes move 32 tons with each lift compared to a maximum 8 tons for a forklift, saving not only time, but also significant labor and capital costs. It is also possible to drive the cranes manually, assisted by Konecranes Smart Features for positioning and safety. In addition, the crane system has an interface for personnel access control to prevent people from entering the working area when cranes are operating in automatic mode.