Discover the benefits of the Pull System in industrial material handling as this article explains its implementation considerations and advantages. Learn how it differs from traditional push systems, emphasizing the significance of designing processes based on actual consumption. Explore the advantages of reducing overstocking, improving responsiveness to customer demands, and achieving just-in-time delivery. The article also examines Konecranes Agilon as an exemplary automated warehouse solution.
“The more inventory that a company has, the less likely they will have what they need.” /Taiichi Ohno/ [The Toyota Way, 14 management principles from the world´s most significant manufacturer]
Konecranes Agilon warehouse automation is a unique solution to implement a replenishment process controlled by the customer. With Agilon, the need is created automatically by using material management data.
Agilon can handle all the needed transaction phases, including delivered POs to vendors and goods received at the buyer’s site
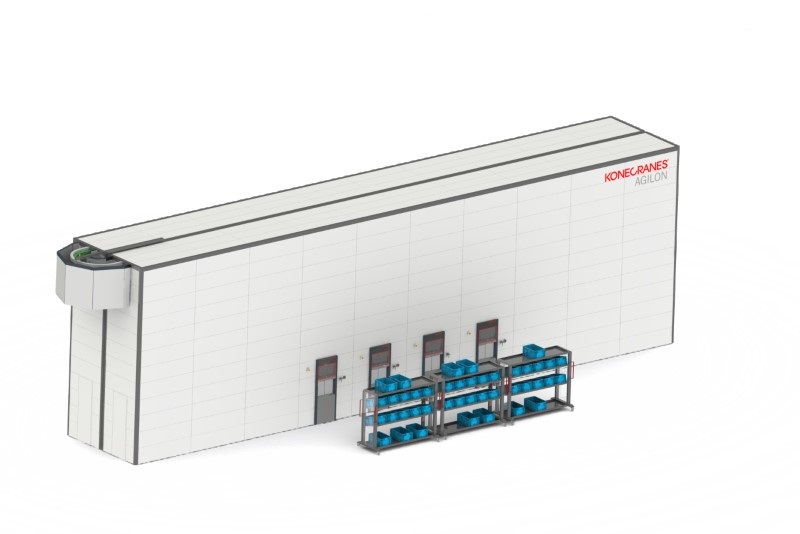
Agilon can handle all the needed transaction phases, including delivered POs to vendors and goods received at the buyer’s site. Agilon can control the material usage and how much is taken out and delivered. According to LEAN- principles, Agilon allows managing the supplier base without vendor integration into factory material management.
When the customer owns the replenishment process, the vendor's role is only to feed the process with the items. There are also some technical solutions for these cases in the marketplace. The feature is available in some ERP systems.
There are two major principles to managing material flow: PUSH and PULL.
There are two major principles to managing material flow: PUSH and PULL. Traditionally, PUSH systems try to predict the future and design a perfect process. As a result, the correct stock levels, the replenishment schedule, and the quantity is calculated together into an ideal process flow. Input for such calculations includes the planned production level, bill-of-material (BOM) and the delivery times of the supply chain. This predictive calculation, or Material Resource Planning (MRP), can be complicated and time-consuming. PUSH systems' weaknesses include a slow reaction time to demand, production process or supply chain changes. This can lead to problems like overstocking, increased work-in-progress (WIP), or an inability to meet customer demands.
PULL systems, on the other hand, are designed based on actual consumption instead of predicted consumption.
PULL systems, on the other hand, are designed based on actual consumption instead of predicted consumption. Just-in-time (JIT), fitting parts, and the amount at the right place when needed. That is what The Toyota Production System (TPS) has advised us to aim for now for decades. TPS lists five focus areas in the process design to make it work and be honest.

Figure 1 The Toyota Production System (The Toyota Way – Jeffrey K Liker 2004). Pull system as a part of the Toyota Production System concept.
- Plan production flow based on selected Takt Time. This gives a framework for controlling utilization and capacity in the process.
- Continuous Flow means that the material flow is process driven and planned for the minimum waiting time before the next phase.
- In Pull System, replenishment and process are controlled by a consumption impulse. At the end of the line, it is tricked by the customer's need. This paper describes pull systems in more detail.
- Making the production process agile requires Quick Changeover.
- Integrated Logistic chain means reducing gaps in the logistic chain.
The pull system works well when there is a balance between the market demand and the cost of agility for the business to tolerate changes.
TPS teach us to use Pull System to avoid overproduction. The basic principle is that the customer needs to launch a pull impulse. This impulse then indicates a need for a component replenishment. The material flow is controlled with parameters like replenishment schedule and batch size to meet the customer demand. The design principle aims to obtain a stable process within specific agility tolerances. Agility control becomes more critical to regaining process efficiency if greater changes are required. The pull system works well when there is a balance between the market demand and the cost of agility for the business to tolerate changes.
Typically, the pull is created using visual Kanban elements, like cards and containers.
Typically, the pull is created using visual Kanban elements, like cards and containers. These elements signal a need for replenishment after consuming a batch of items or parts. For example, an empty bin in the production cell is an indication for the warehouse to replenish.
Several Kanban elements in the process control production volume. One more Kanban element is added to the production if the market grows. When the demand decreases, elements are reduced. Literature calls this adjustment quantitative ability.
When the product changes, item contents and bill-of-material are altered to meet the new requirements. This is called qualitative ability. In a visual Kanban process, one change might require several changes on the factory floor. Cards and bins must be adjusted to the new situation.
Implementing control using quantitative and qualitative changes is essential to operational excellence in material handling.
Agility in the process creates competitiveness. Implementing control using quantitative and qualitative changes is essential to operational excellence in material handling.
Typically, Kanban is used for low-value processes. MRP tools and principles are more likely to be applied in sourcing high-value items. For asset management reasons, the stock balance and timing are more critical in material planning. The lead time is affected by, for example, when purchase orders are placed against sales orders. The cost of managing the purchases increases the transaction costs. For high-value items, this can be justified. However, for low-value items, the transaction costs might be too high. High transaction costs are why several solutions in the marketplace streamline the transactions between the vendor and the customer.
Demand for profit is justified because the vendor carries the risks and the costs related to making the items available just in time.
When designing a pull system crossing the customer-vendor boundary, it is important to realise who owns the process. Often, the replenishment process is part of the vendor’s product. The customer’s business is thus based on the costs of direct line feed and the item price. In this case, the vendor owns the process. Demand for profit is justified because the vendor carries the risks and the costs related to making the items available just in time.
When looking for alternatives for pull systems in industrial material handling, challenge your current knowledge. Make sure to check the latest in the market: Maximum throughput and 100% picking accuracy with Agilon® warehouse automation | Konecranes
For more information, please contact Vesa Hämetvaara, Director, Konecranes Agilon.
Email: [email protected]