Fast, accurate and efficient production processes and less internal logistics
Agilon handles order picking, registers every transaction and ensures that the production warehouse contains the required quantities of products for all work phases. The system displays the work queue and quickly brings users the needed parts and orders.
Smooth work management makes it easy to manage changes to production plans, as Agilon does not need help with warehouse or picking planning. It organises itself dynamically to meet the changing needs of production. Agilon standardises the picking process, speeding up new employee orientation.
The automated warehouse makes processes more efficient and reduces the time spent picking. With Agilon and without picking errors, the balances always remain 100 % accurate. The total balance and inventory accuracy in the warehouse of thousands of components enables timely operational purchases from suppliers.
ABB implemented the Agilon batch picking feature
ABB Oy's Smart Power unit in Vaasa implemented the Agilon batch picking feature as soon as it was available.
Batch picking saves considerable time.
"Batch picking saves considerable time because we have many of the same work orders from Agilon, which often contain the same components. Our warehouse workers have been delighted with this functionality and its clarity and ease", says Planning & Fulfillment Specialist Aleksi Laitinen from ABB Smart Power.
Agilon batch picking with a light-controlled trolley meets the challenges of small goods logistics.
Agilon warehouse automation has comprehensively solved the challenges of internal logistics in the past, but now Konecranes has raised the picking speed to its peak without compromise. Productivity and efficiency are critical to the operations of any modern production plant. Agilon optimises production lines with accurate and efficient picking. Batch picking with the put-to-light trolley guides workers seamlessly through the picking process, enabling a safe and ergonomic environment. Agilon batch picking with the put-to-light trolley guide workers seamlessly through the picking process, fostering a safe and ergonomic environment.
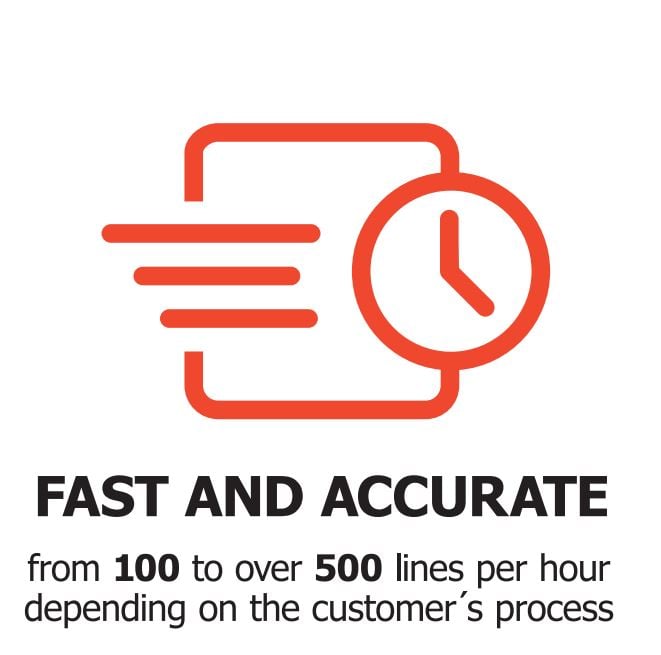
Agilon is easily scalable if production needs and production layout change. Automated warehouse Agilon occupies less space than traditional shelving solutions, and intralogistics functions are clear and smooth. In addition, time-to-completion – from assembly to the order dispatch and installation is short.
Tracked and traced quality management
Every transaction Agilon completes is traceable as every item entered into or removed from the system is user, time, and date stamped. Every item is backed up with a digital photograph from the latest retrieval or replacement to the system.
The data generated by the Agilon system provides opportunities for developing quality, procurement and operating methods more diversely than was previously possible.